Sterile-to-Sterile vs API-to-Sterile Compounding: Making the Best Choice for Your Patients
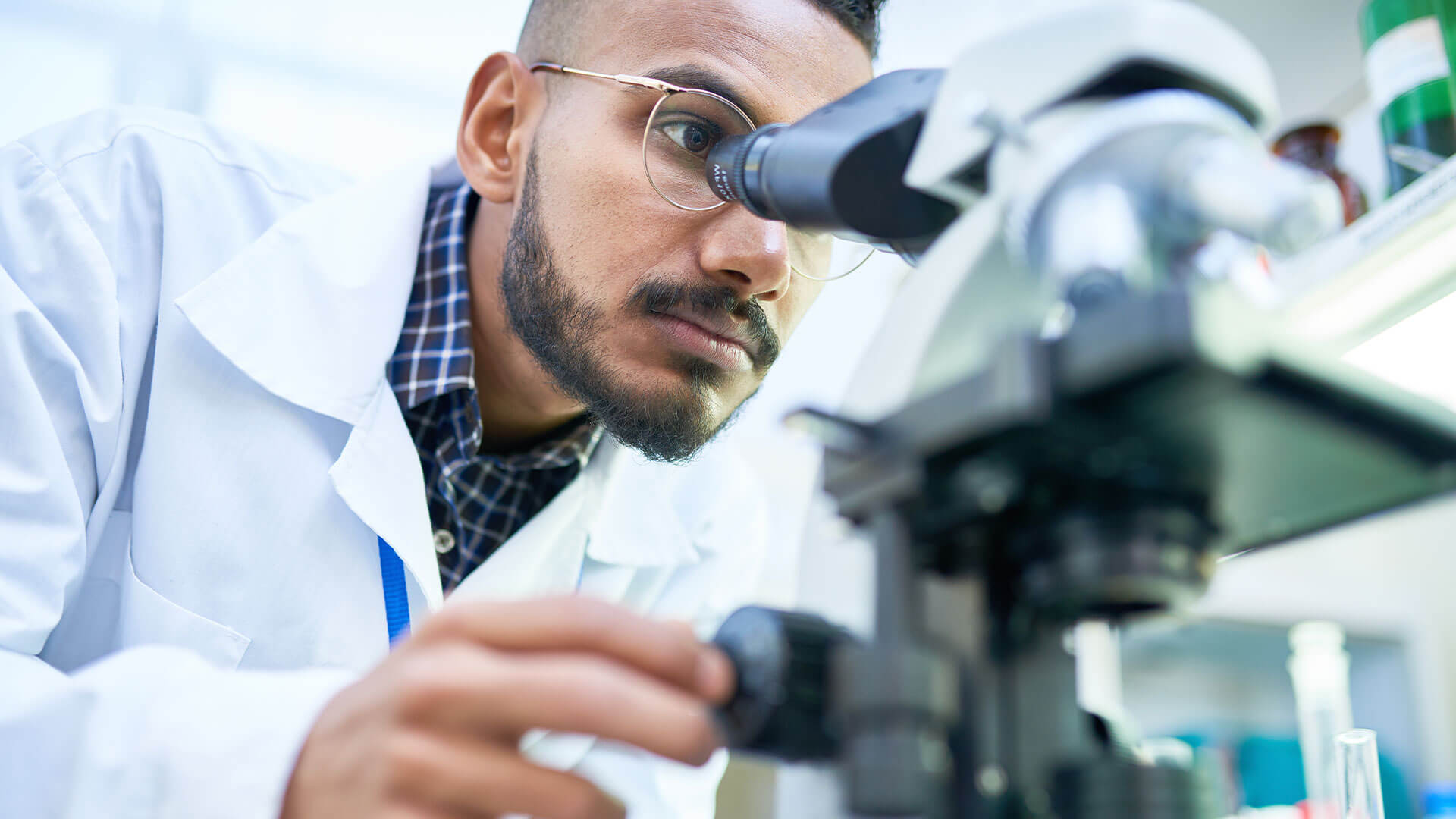
Are you a pharmacy manager or administrator who is responsible for maintaining the availability of pharmaceutical products for your ambulatory surgery center (ASC), health system, hospital, or physician's office? Are you concerned that your healthcare providers lack a good supply of injectables, ophthalmic solutions or operative anesthesia so that they can provide high-quality care to their patients?
You are likely overwhelmed by frustrations and fears of drug shortages that are interfering with your ability to provide proper patient care. It is particularly difficult to keep compounded sterile preparations (CSPs) in stock. The global pandemic brings fears of supply chain breakdown into sharp focus.
"We have seen this recently with the unavailability of sedatives and muscle relaxants for COVID-19 patients requiring mechanical ventilation. Drug manufacturers and sterile-to-sterile outsourcing facilities have not been able to supply market needs, whereas API-to-sterile outsourcing facilities have been successful in providing those needed drug products." Carl Woetzel - President, President, Fagron Sterile Services US (FSS). [1]
Not only are health care systems buckling under the pressure of treating patients with COVID-19, but healthcare consumers are also becoming increasingly unable to delay their elective surgeries and pain management interventions. In this post, we present a solution that will allow hospital systems to react to sudden changes in CSP needs while still preventing the monetary waste of being overstocked. A nimbler, more strategic approach is necessary.
A Solution in 503B Outsourcing Facilities
The Drug Quality and Security Act (DQSA) was enacted in 2013. It authorized the US Food and Drug Administration (FDA) to establish Section 503B. One of the results was the 503B outsourcing facility. The DQSA prompted major changes in other federal laws regarding bulk drug substances, drug compounding and the subsequent progression to large-batch, commercialized drug products. Regulators, politicians, healthcare providers, and pharmaceutical industry leaders worked together in making compounded medications more available and safe for patients. [2]
Top tier 503B compounders are in an excellent position to provide sterile and non-sterile drug products to patients that are not normally commercially available. Although Fagron can achieve this goal by supplying sterile-to-sterile drug preparations; we have found that we can best serve many of our customers by first procuring active pharmaceutical ingredients (API) that are processed and tested in our highly-regulated manufacturing facilities; then labeled and packaged for release to customers. By overseeing the complete end-to-end compounding process, we can guarantee quality assurance and reliability of all available drugs, which supports patient safety.
Sterile-to-Sterile Compounding
In sterile-to-sterile compounding, the 503B outsourcing facility receives the sterile products as merely another entity along the supply chain, rather than keeping all processes in-house. The sterile preparations are manufactured by the pharmaceutical company, shipped to the wholesaler, purchased by the 503B outsourcing facility, repackaged, and finally shipped to their final destination. This reliance on multiple intermediaries can oftentimes drive up prices and compromise availability of critical compounded preparations.
Jason Winfield, Vice President of Operations - FSS, effectively describes other disadvantages of sterile-to-sterile compounding including the following:
- "Requires sourcing of pharmaceutical vials or ampules; generally will drive costs higher, and lack of availability during drug shortages results in no products to healthcare providers.
- The sterile-to-sterile process requires the 503B outsourcing facility to manipulate and pool 100’s of vials/amps during a process, resulting in potential for particulate contamination and issues with coring.
- Lack of sterile filtering offers an opportunity for poor aseptic practice and operator contamination."
API-to-Sterile Compounding
With all compounding processes centralized under one 503B outsourcing facility, fewer steps are needed to manufacture the needed drug preparations. The final compounded product reaches the final recipient much more quickly. The entire process is vertically integrated, while still complying with all federal laws and quality control standards.
Jason Winfield -
- "Fagron manufactures all drug products to “standard” pharmaceutical industry expectations.
- API is sourced from FDA approved and registered vendors, who are audited by Fagron annually.
- Manufacturing processes are engineered, validated, and proceduralized for robustness and consistency. Every detail of the process is defined in standard operating procedures, and master batch records (unique for each process). The SOPS & MBRs are followed and any deviation from these processes results in a deviation investigation to determine root cause and impact prior to batch disposition.
- The manufacturing environment is continuously inspected per FDA rules on environmental monitoring (temperature, humidity, air pressures, HEPA flow, viable and non-viable particulate) & people are routinely monitored on a batch-specific basis.
- All batches are sterile-filtered, and filter integrity tests confirm successful terminal filtration.
- Each batch undergoes rigorous quality inspection, critical system confirmation, sterility, potency, and other required compendial testing which is product specific.
- Quality and aseptic (ISO class V) processes are routinely monitored to confirm adherence to all site procedures."
In short then, compounded sterile preparations (CSPs) are easier to manufacture and maximize availability when API-Sterile procedures are used.
Carl Woetzel - "While both sterile-to-sterile and API-to-sterile compounding processes result in the production of safe products, we believe that the safety, efficiency, and invulnerability to drug shortages inherent in API-to-sterile-compounding renders it a worthwhile choice."
Current Good Manufacturing Practices (cGMP)
[3] Unlike 503A compounding pharmacies, 503B outsourcing facilities are required to comply with cGMP as mandated by the FDA (21 CFR Parts 210 & 211). This is the case for both sterile-to-sterile and API-to-sterile compounding activities.
Under cGMP, an extremely robust series of required procedures are needed to assure safety and quality of the final drug preparations. The regulations are much more stringent than those of the United States Pharmacopeia (USP). Compounded drugs manufactured under section 503A are not bound by cGMP federal laws (however they still must comply to USP standards and state boards of pharmacy).
503B outsourcing facilities are inspected for documentation of the following:
- Daily environmental monitoring
- Beyond Use Date (BUD)
- Sterile Disinfecting
- Continuous Particle Counts
- Sterility and Stability Testing
- Sterile Garb [for pharmacy technicians and other staff]
The cGMP is considered a global model of good practice among drug manufacturers, compounders, regulators, and pharmaceutical industry health care providers. This includes adoption of the "cGMP Mindset." It is described as a series of attitudes, actions, and behaviors necessary for a sound pharmaceutical compounding process. The effective cGMP is modeled by leadership and embraced by a strong organizational culture.
Carl Woetzel, "Fagron has purposefully hired expertise in cGMPs and sterile pharmaceutical manufacturing, quality operations and technical services to uniquely position us to support hospitals, health systems and their leadership in delivering cost-effective, high-quality and reliable ready-to-use sterile injectables."
Oversight of the Total Process
There are times when a customer may prefer the sterile-to-sterile compounding option. As stated earlier, a trustworthy, customer-service oriented 503B outsourcing facility will surely have both options in their portfolio (See FSS’ article on moxifloxacin). The key message is that API-sterile compounding completed by a top tier 503B outsourcing facility such as Fagron is just as safe as sterile-to-sterile compounding. Oversight of the total process results in multiple benefits, including maximum quality, expedience, cost-management, and availability.
Carl Woetzel, "This often comes down to customer preference. However, I believe there are several advantages to API-to-Sterile compounding. For instance, drug shortages often affect the availability of a medication needed in an ASC. If an ASC chooses to partner with a 503B that manufactures from API, the likelihood of experiencing supply interruptions in the face of a drug shortage can be reduced. Another advantage is that the manufacturing process is more efficient and requires fewer steps to get to the final drug product. 503Bs that pursue only Sterile-to-Sterile compounding are required to purchase finished pharmaceutical goods which have been manufactured by a pharmaceutical company, shipped to a wholesaler, ordered by the 503B and then repackaged and sold to the customer. A 503B that uses API acts as a drug manufacturer and produces drug products directly for their customer."
Advantages of API-to-sterile Drug Preparations
- Minimization of supply chain disruptions of approved drug.
- Cost savings from cutting out intermediaries is passed on to our customers.
- Greater transparency and more personalized service.
- Because all critical processes are completed by a single entity; this creates assurance that drug products are indeed manufactured with cGMP, USP, and all regulations pursuant to the Federal Food, Drug, and Cosmetic Act.
- End-to-end manufacture of drugs on FDA approved drug lists that are consistently in their proper dosage forms.
- Quality assurance and quality control is easier.
- Vertical integration strategies allow more responsive management of drug shortages.
- Easier for high-risk CSPs to be used within the recommended 24 hours. (4)
Conclusion
Carl Woetzel: "While both sterile-to-sterile and API-to-sterile compounding processes result in the production of safe products, we believe that the safety, efficiency, and invulnerability to drug shortages inherent in API-to sterile compounding renders it a worthwhile choice."
That being said, Fagron Sterile Services US will gladly continue to provide API-to-sterile as well as sterile-to-sterile compounded products to its customers.
You may have more questions about API-sterile compounding. We invite you to contact us or speak with a personal representative today.
Sources:
1 Fagron Sterile Services. (June 2, 2020). How ambulatory surgery centers (ASCs) can benefit from pharmaceutical outsourcing facilities: 8 questions answered.
(This article was used throughout the content (per client request)- but only cited once to keep the visual presentation of the content cleaner.
2 PEW Charitable Trust (2014, May 21). Ensuring the safety of compounded drugs: Study highlights key quality standard.
3 Clinical IQ. Quality Standard for Large-Scale Manufacturing Facilities.
4 Gudeman, J., Jozwiakowski , M., Chollet, J., Randell, M., (2013).Potential risks of pharmacy compounding. Drugs R D 13:1–8 DOI 10.1007/s40268-013-0005-9.